At Rawside, we don't just design and build furniture, we craft lasting pieces that bring spaces to life. Every table, shelf and product you see starts with a spark of creativity and moves through the hands of skilled designers and makers who care about sustainability, style, durability and substance.
Let's take you behind the scenes.
Let's take you behind the scenes.
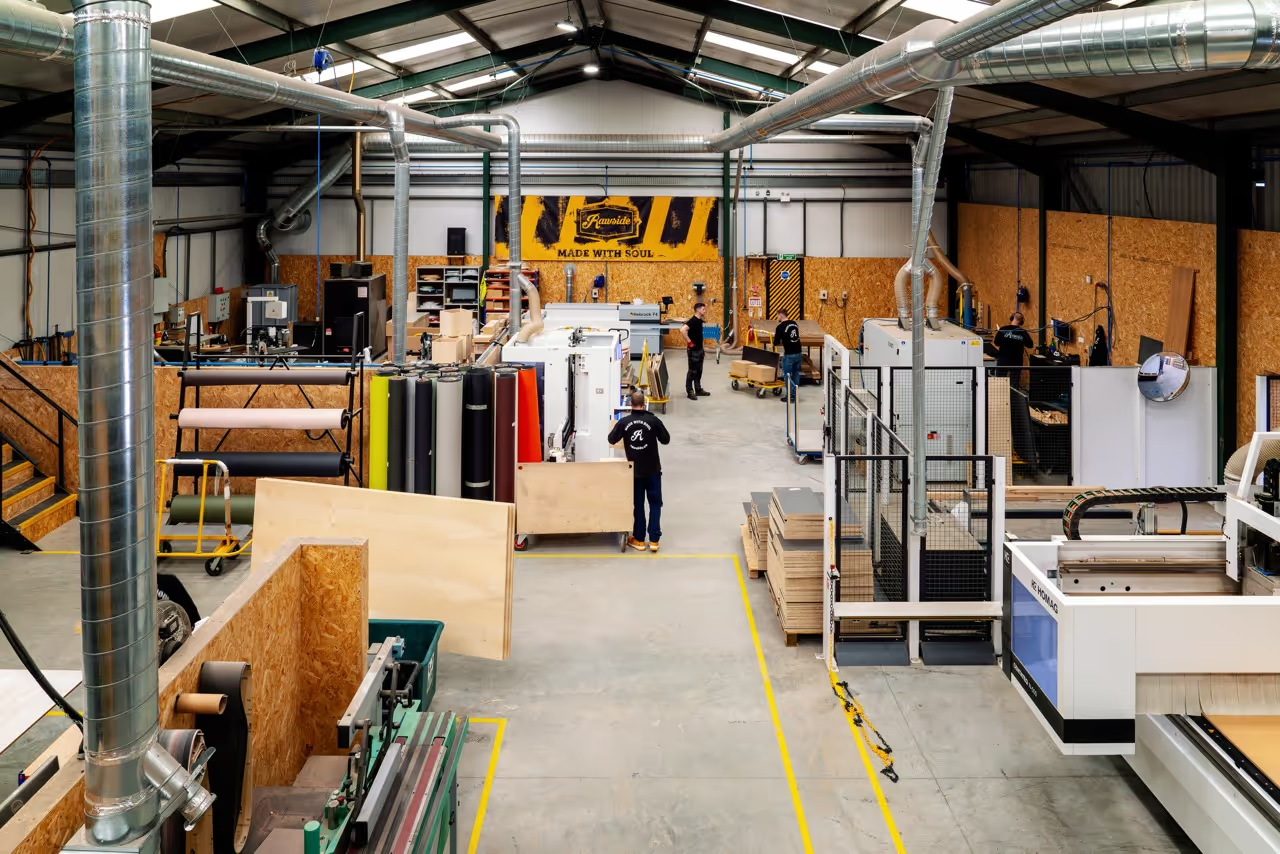